При повышении напряжения (разности потенциалов), приложенного к изоляции, наступает критическое значение напряжения, при котором изоляция пробивается. Это значение напряжения именуется пробивным напряжением, а свойство изоляции выдерживать длительно определенное напряжение называется электрической прочностью.
Пробивное напряжение относят обычно к 1 мм (или 1 см) толщины изоляции. С повышением температуры электрическая прочность снижается, так, например, электрофарфор при перепаде температуры от 20 до 100°С снижает электрическую прочность на 30% и практически теряет электрическую прочность при 350°С.
Наличие воздушных прослоек в изоляции приводит к ионизации воздуха и снижению электрической прочности изоляции.
Влажность материала также значительно снижает электрическую прочность, так, например, при влажности трансформаторного масла 0,01% пробивное напряжение снижается с 20 до 6,4 кВ/мм.
Обычно в трансформаторах малой мощности (за некоторыми исключениями) запас по пробивному напряжению очень велик, но может быть тепловой или электрохимический пробой.
Электроизоляционные материалы не должны пропускать ток. Практически, находясь под напряжением, они пропускают незначительный ток, называемый током утечки. Величина этого тока определяется приложенным напряжением и сопротивлением изоляции.
Ток утечки, проходя по изоляции, нагревает ее, что приводит к снижению пробивного напряжения. Помимо этого, при прохождении тока утечки в изоляции развиваются электрохимические процессы, приводящие к уменьшению сопротивления изоляции (старению изоляции) и еще большему увеличению тока утечки. В конечном результате это приводит к тепловому пробою (за счет нагрева изоляции) или к электрохимическому пробою. Ускоряет старение изоляции наличие влаги в атмосфере и в очень большой степени — наличие активных газов.
Токи утечки могут проходить как через толщу материала, так и по его поверхности. Величина тока, проходящего через толщу материала, определяется его объемным сопротивлением, проходящим по его поверхности, — поверхностным сопротивлением. Удельное объемное сопротивление ρv, Ом • см численно равно сопротивлению в Омах кубического сантиметра материала при напряжении, приложенном к двум противоположным граням двумя электродами площадью 1 см2. Последние имеют плотный контакт с гранями кубика. Поверхностное сопротивление боковых граней кубика исключается схемой испытания.
Удельное поверхностное сопротивление ρs, Ом, равно сопротивлению квадрата на поверхности материала между электродами, имеющими контакт с противоположными сторонами квадрата (сопротивление не зависит от размера квадрата).
Объемные сопротивления различных изоляционных материалов - диэлектриков составляют величины от 109 до 1020 Ом • см, поверхностные — от 108 до 1018 Ом. Объемное сопротивление более стабильно. Во влажном воздухе диэлектрики в зависимости от гигроскопичности снижают свое объемное сопротивление, впитывая влагу. Скорость впитывания может колебаться в очень широких пределах; от часов (для непропитанных хлопчатобумажных материалов) до месяца и более.
Поверхностное сопротивление быстро реагирует на изменение влажности воздуха. Кроме того, оно в значительной степени зависит от характера поверхности материала и его запыления. На глянцевой поверхности меньше оседает влаги, и она меньше подвержена загрязнению.
Гигроскопичность изоляционных материалов определяется по количеству влаги (в процентах к весу материала), которую впитывает данный сухой материал, помещенный в насыщенную водяными парами атмосферу (обычно при температуре 20° С на время 24 ч). Для некоторых материалов важна степень влагопоглощаемости, которая определяется аналогично гигроскопичности, но при помещении материала в дистиллированную воду. В отдельных случаях определяется и гигроскопичность и влагопоглощаемость.
Большинство материалов обладает смачиваемостью. Капля воды на поверхности материала растекается в большей или меньшей степени (в зависимости от смачиваемости данного материала). Эти материалы называются «гидрофильными». Если капля растекается равномерно по всей поверхности, смачиваемость называют «абсолютной».
Другая группа материалов называется «гидрофобными» (в обиходе «водоотталкивающими»). К ним относится группа так называемых «воскообразных» диэлектриков и некоторые другие. На их поверхности влага собирается мелкими каплями (как капли ртути на стекле), образуя прерывистую пленку. На рисунке 1 приведены сравнительные характеристики поверхностных сопротивлений для некоторых типов диэлектриков.
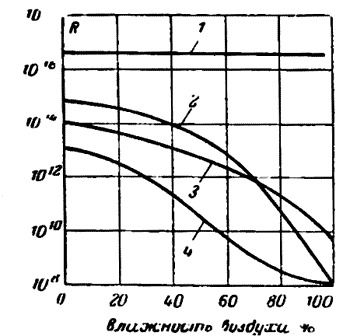
1 — парафин; 2 — шеллак: 3 — стеклолента (непропитанная); 4 — фарфор Рисунок 1 - Зависимость поверхностною сопротивления изоляционных материалов от влажности воздуха
Гидрофобные диэлектрики хорошо предохраняют обмотки от действия влаги. Возможности их применения в тех или иных случаях определяются их остальными свойствами.
Одно из основных свойств диэлектриков, с которыми приходится сталкиваться при изготовлении малых трансформаторов, — это теплопроводность. Коэффициент теплопроводности (называемый также «удельная теплопроводность») определяется количеством тепла в ваттах, которое проходит через кубический сантиметр данного материала от одной грани к противоположной при разности температур между этими гранями 1°С. Выражается коэффициент теплопроводности в ваттах на 1 см на 1°С, может быть выражен в джоулях или калориях (1 Вт/см • °С = 1 Дж/см сек • °С = 0,2389 кал/см • сек • °С).
Помимо требований надежности и других дополнительных требований, определяющих применение тех или иных электроизоляционных материалов, при выборе последних необходимо учитывать климатические и другие местные условия. По условиям работы аппаратура может иметь следующие исполнения.
Нормальное исполнение предназначено для работы аппаратуры в условиях нормальной влажности при отсутствии в воздухе активных газов, температура воздуха от +25 до +45°С, т. е. в основном для аппаратуры, работающей в закрытых и отапливаемых помещениях. В тех случаях, если эти изделия имеют наиболее низкий уровень надежности, как, например, многие технические устройства, неответственные электронные устройства и другие устройства широкого профиля, обмотки трансформатора обычно не пропитываются, что упрощает и удешевляет их изготовление и ремонт. Но в различных испытательных, нагрузочных и других устройствах (в основном предназначенных для разъездных работ), трансформаторы которых часто могут работать в форсированном режиме, обмотки независимо от требуемого уровня надежности следует пропитывать теплостойкими лаками. Это увеличивает теплопроводность обмоток и способствует повышению возможности их форсировки. Обмотки трансформаторов всех устройств, к которым предъявляются повышенные требования надежности, следует обязательно пропитывать. Это значительно повышает также и долговечность изделия.
Влагостойкое исполнение особенно необходимо в местах с жарким и сырым климатом. Количество влаги в воздухе зависит от температуры воздуха и от степени влажности. В 1 м3 воздуха при его насыщении находится воды в виде пара при температуре 0; 20; 40; 60° С соответственно 6; 24; 75; 130 г. Нормальной влажностью считается воздух, содержащий 60—65% влаги от предела насыщения, сырым — содержащий более 80%, сухим — менее 40%. При повышенной температуре воздуха нормальной влажности соответствует значительно большая абсолютная влажность, т. е. количество влаги в 1 м3 воздуха.
При охлаждении воздух нормальной влажности становится пересыщенным и избыточный пар оседает в виде капель в порах обмотки, в зазорах стали магнитопровода, вызывая необратимое электрохимическое разрушение изоляции и коррозию стали магнитопровода и меди обмоток, часто приводящую к разъеданию и обрыву проводов (особенно частых при диаметрах менее 0,1 мм). Влагостойкое исполнение следует применять к обмоткам на гидроэлектростанциях, на торфяных болотах, в насосных, котельных. Применением соответствующих пропиток можно значительно снизить действие влаги.
Химостойкое исполнение применяется при наличии в воздухе активных газов. Последние приводят к таким же разрушениям, к каким приводит влага, но процесс протекает значительно интенсивнее, особенно в сочетании с влагой. Химостойкое и тропическое выполнения примерно аналогичны. В обоих случаях хлопчатобумажные и целлюлозные материалы, а также провода ПЭЛ, ПЭЛУ, ПЭВ-2 не применяются. Применяются стеклоткани и стеклотекстолиты. Предъявляются более повышенные требования к пропиточным лакам.
Для тропиков, кроме того, учитывают специфичные для тех или иных областей реагенты, в том числе микроорганизмы, разрушающие некоторые электролаки и материалы. В ряде случаев необходима консультация химиков.
При влагостойком, химостойком (и тропическом) выполнении пропитка всех обмоток обязательна, режимы нагрева трансформатора должны быть снижены.
К волокнистым электроизоляционным материалам относятся изделия хлопчатобумажные, шелковые, из древесной целлюлозы, а также нагревостойкие из стекловолокна и асбестового волокна.
Материалы первой группы, применяемые без пропитки, относятся к классу нагревостойкости У, допускающему максимальную температуру не свыше 90° С. Следует указать, что целлюлозные материалы разлагаются в присутствии кислорода воздуха и при нормальной температуре, но за время, исчисляемое годами. При температуре выше 90° С процесс разложения резко убыстряется. Пропитка заполняет поры в этих материалах, уменьшая значительно поверхность соприкосновения с воздухом.
Из второй группы нагревостойких волокнистых материалов широкое применение нашли стекловолокнистые изоляции, имеющие высокие электрические свойства, малую гигроскопичность и высокую прочность. Асбестовые волокнистые материалы в качестве электроизоляционных материалов почти полностью вытеснены стекловолокном.
Из древесной целлюлозы и хлопчатобумажного волокна изготовляются картоны ЭВ (электрокартон воздушный целлюлозный) и ЭВТ (то же тряпичный) и другие картоны для работы в масле. Картоны изготовляются толщиной от 0,1 до 3 мм. В бытовых трансформаторах обмоток применяются для изготовления каркасов для обмоток.
Из бумаг применяются кабельная марок К-08, К-12, К-17 (толщиной 0,08; 0,12; 0,17 мм) для межслойных и межобмоточных прокладок в обмотках, конденсаторная марок от А-7 до А-24 (от 7 до 24 мк), часто используется бумага от разобранных конденсаторов, пропитанная церезином или головаксом. Пропиточная бумага толщиной 0,12 мм может быть рекомендована для межслойных прокладок в обмотках, подлежащих пропитке.
Хлопчатобумажное волокно применяется для изготовления лент и электроизоляционных тканей. Ленты: киперная (толщиной 0,54 мм), тафтяная, миткалевая, батистовая (0,22 мм). При изготовлении малых трансформаторов батистовая лента иногда применяется для оплетки галетных обмоток.
Из электроизоляционных тканей применяются в основном: перкаль в производстве лакотканей, миткаль и бязь в производстве текстолита. Шелковая ткань иногда применяется для межслойной и межобмоточной изоляции (с последующей пропиткой), чаще применяется шелковая лакоткань. Ткань типа шифон применяется в производстве текстолита марки ВЧ.
Стекловолокно применяется для изготовления лент и тканей. Ленты изготовляются толщиной 0,1 мм (и тоньше) при ширине от 8 до 25 мм, ткань изготовляется толщиной от 0,1 до 0,06 мм, для специальных изделий до 0,025 мм. Для электроизоляции применяется бесщелочное волокно. В таблице 1 приведены для сравнения некоторые данные непропитанных лент и электрические данные для сухих лент. Таблица 1
Параметры и свойства | Лента стеклянная | Лента хлопчатобумажная | Лента асбестовая |
Ширина, мм | 25 | 25 | 25 |
Толщина, мм | 0,12 | 0,2 | 0,4 |
Гигроскопичность, % | 0,98 | 18 | 6,9 |
Водопоглощаемость, % | 11,8 | 85 | 75 |
Прочность на разрыв, кГ/мм2 | 19,8 | 3,6 | 0,96 |
Объемное сопротивление ρv, ом·см | 1014 | 108 | |
Поверхностное сопротивление ρS, ом | 1012 | 107 | 3·106 |
Хлопчатобумажные лакоткани имеют марки ЛХС, ЛХCM, ЛХСС, ЛХЧ; толщина лакоткани от 0,15 до 0 24 мм. Шелковые (капроновые) лакоткани имеют марки ЛШС, ЛШСС, ЛКС, ЛКСС, толщина от 0,05 (ЛШСС) до 0,15 мм. Нагревостойкость лакотканей относится к классу А.
На основе стеклоткани выпускаются лакоткани марок ЛСМ, ЛСММ с нагревостойкостью класса А. Лакоткани марок ЛСЭ и ЛСБ имеют нагревостойкость класса В, марки ЛСК, ЛСКЛ, ЛСКР (на кремнийорганическом лаке) имеют нагревостойкость класса Н. Толщина стеклотканей от 0,11 до 0,24 мм, за исключением марки ЛСК, имеющей толщину от 0,05 мм.
Стеклолакоткани с нагревостойкостью класса Н в условиях эксплуатации выдерживают температуру до 200° С, а кратковременно в течение 2—3 ч — до 250° С.
Помимо этих марок стеклотканей, выпускаются марки по техническим условиям министерств и заводов.
Для бытовых трансформаторов применяются хлопчатобумажные и шелковые лакоткани. Для трансформаторов, к которым предъявляются высокие требования надежности, рекомендуется применять стеклолакоткани. Для сырых помещений можно применять лакоткань ЛХЧ (черная) с масляно-битумной пропиткой. Эта лакоткань не маслостойка, но она более влагостойка и меньше склонна к старению, чем светлые хлопчатобумажные и шелковые лакоткани.
Широкое применение имеют прессованные слоистые материалы, состоящие из нескольких слоев основы, пропитанной соответствующими смолами (лаками) и спрессованными при определенных температуре и давлении. В качестве основы применяют древесные и растительные волокна, стекловолокно, асбестовое волокно.
При изготовлении каркасов для обмоток в основном применяют листовые материалы, состоящие из нескольких слоев бумаги или текстиля, пропитанных лаками на основе бакелитовых смол.
Первые называются гетинаксами, вторые — текстолитами. Листы гетинакса и текстолита изготовляются толщиной от 0,5 до 50 мм. Текстолит лучше подвергается штамповке, но его электрические свойства ниже, кроме того, он значительно дороже. Обычно применяют гетинакс следующих марок: В — для работы в масле и на воздухе, повышенной механической прочности; Г — для работы на воздухе в условиях повышенной влажности; ВС — для работы на воздухе, с повышенными электрическими свойствами.
Из текстолитов применяются следующие марки: А — для работы в масле и на воздухе; Б — для работы на воздухе, повышенной механической прочности; Г — панельный.
Кроме этих марок гетинакса и текстолита, изготовляются другие марки для работы в масле и для устройств высокой частоты.
При специальных требованиях к трансформатору следует выбирать соответствующую марку. Для бытовых трансформаторов применяют любую марку гетинакса или текстолита.
Объемное сопротивление различных марок гетинакса ρv = 109—1012 ом·см, текстолита ρv = 109—1010 ом·см.
Гетинаксы и текстолиты предназначены работать при температуре окружающей среды от минус 60 до плюс 70° С. Допустимая рабочая температура гетинакса 120° С, выдерживает температуру 140° С, при 150° С может отслаиваться. Для гетинакса марки ВЧ и большинства марок текстолита рабочая температура 105° С. Влагопоглощаемость гетинаксов и текстолитов менее 0,5%. Следует иметь в виду, что ГОСТ указывает влагопоглощаемость по количеству впитанной воды (за 24 ч) в граммах к площади 1 дц2, а не в процентах к весу материала.
Стеклотекстолиты выпускаются электротехнических марок СТ, СТУ, СТК, СТЭФ, СТЭП и конструкционный нескольких марок. По электрическим свойствам лучшими марками являются СТК и СТ/ЭП. Стеклотекстолиты отличаются высокой механической прочностью и низкой гигроскопичностью.
Сопротивление стеклотекстолитов марок СТК и СТ/ЭП составляет ρv = 1014 ом·см, ρs=1014 ом. Объемное сопротивление остальных марок ρv = 1012 ом·см. Допустимая рабочая температура 180° С. Кратковременно выдерживают до 250° С.
По назначению электролаки различают: пропиточные, покровные и клеящие.
Пропиточные лаки служат для пропитки обмоток и заполнения пор в обмотке, как в волокнистой изоляции проводов, так и воздушных межвитковых и межслойных пор. Это способствует снижению гигроскопичности, увеличивает теплопроводность и электрическую прочность, при этом снижается старение материалов, следовательно, повышается долговечность и надежность обмотки.
Покровные лаки, создавая на обмотке гладкую и глянцевую поверхность, улучшают циркуляцию воздуха и конвекцию тепла обмотки в окружающую среду, дополнительно повышают влаго- и химозащиту, повышают механическую прочность обмотки и улучшают внешний вид.
Клеящие лаки служат для склеивания различных материалов. Они должны иметь высокие электроизоляционные свойства при высокой клеящей способности.
При пропитке должны заполняться все поры в обмотке, для чего пропиточные материалы должны иметь малую вязкость. В оставшихся порах ионизация, воздуха вызывает местное старение изоляции и снижение электрической прочности. Для трансформаторов малой мощности с относительно малыми напряжениями (за редкими исключениями) это не представляет опасения, что значительно облегчает пропитку таких обмоток. При этом может быть лишь незначительное снижение теплопроводности.
Пропиточные материалы делятся на две группы:
1) компаунды, к которым относятся битумы, битумно-масляные лаки, воскообразные материалы, а также синтетические лаки без растворителей. Компаунды при пропитке находятся в жидком состоянии и застывают при охлаждении (термопластичные) или в результате происходящих в них при нагреве химических изменений (термореактивные), при этом переходят в неплавкое и нерастворимое состояние (полимеризуются). Большинство компаундов имеет большую вязкость. Поэтому пропитка ведется под вакуумом, с последующим повышенным давлением. Этот процесс может выполняться только в заводских условиях;
2) электролаки с растворителями в условиях мелких производств (и в любительских условиях) нашли более широкое применение. Эти лаки состоят из основы (пленкообразующие или нелетучие) и растворителя (летучие). Количество летучих составляет 40—60%. При заполнении пор и испарении летучих основа лака заполняет поры не полностью. Пропитку приходится повторять несколько раз, при этом каждая последующая становится более покровной, чем пропитывающей. При первых пропитках теплопроводность обмотки повышается, при последующих несколько снижается за счет увеличения толщины слоя лака на поверхности обмотки.
Для пропиток можно рекомендовать лак 321т (ВТУОАВ 504-015), имеющий температуру сушки 105° С, и лак ПФЛ-8а (ТУ ОАВ 504-022) с температурой сушки 125° С. Оба лака водоэмульсионные, предназначены для обмоток по нагревостойкости классов А, Е, В для нормального, усиленно влагостойкого и тропического выполнения. Эти лаки рекомендуются для пропиток обмоток с эмальизоляцией. Лак МЛ-92 (МГМ-16, ВТУ 13-57) с температурой сушки 120—130° С предназначен для обмоток по нагревостойкости классов А, Е, В, F, не рекомендуется для проводов типа ПЭВ-2, пригоден для эмалевых проводов класса нагревостойкости В, F и может применяться для обмоток химостойкого и тропического выполнения. Лаки К-47 (ТУ МХП 658-55) и К-57 (ТУ ВЭИ 25-57) термореактивные, имеют температуру сушки ступенчатую: 100-120° С, затем 160—200° С; по нагревостойкости — класс Н.
До пропитки следует производить сушку обмоток, выполненных из хлопчатобумажной изоляции, при температуре 100—105° С в продолжение 1 ч. При водоэмульсионных лаках предварительная сушка не требуется.
Для пропитки обмотка, нагретая до 70—80° С, погружается в лак на 10—15 мин (при хлопчатобумажной изоляции до 20—30 мин).
Сушка обмоток производится в сушильных шкафах конвекционным способом обдувкой горячим воздухом. Применяют также сушку инфракрасным излучением лампами марок ЭС-lA, ЭС-2А (старая марка СК-1), ЭС-1, ЭС-2, ЭС-3 (старая марка СК-2). Лампы марки СК-2 — зеркальные с посеребренной колбой. Мощность ламп ЭС-lA и ЭС-2 250 Вт, остальные лампы имеют мощность 500 Вт, напряжение 127 В.
При конвекционном способе сушки испарение летучих начинается с поверхности. При этом создается пленка, препятствующая выходу летучих из глубин обмотки. При инфракрасной сушке прогревается вся обмотка и испарение летучих происходит по всей толще обмотки. При этом значительно сокращается время и повышается качество сушки. Этот способ сушки в мелкосерийном производстве является наиболее простым и экономичным.
Следует остановиться на пропитке обмоток по методу Зондероля. По этому методу обмотка нагревается на 10° С выше температуры кипения растворителя и погружается в лак. При проникновении лака в поры растворитель улетучивается. При этом повышается заполнение пор основой лака, и после пропитки обмотка почти не держит летучих. Значительно ускоряется последующая сушка обмотки. Согласно испытаниям, время сушки после пропитки (для крупных машин) сокращается с 10—15 ч до 1—2 ч, при этом обмотки более долговечны, чем пропитанные погружением. Эмальизоляция должна быть стойка к действию растворителей и к тепловому удару, и, кроме, того, должна быть значительная разница между температурами кипения и самовоспламенения растворителя.
В таблице 2 приведены данные некоторых наиболее часто применяемых растворителей. (Следует указать, что для одинаковых марок лака иногда применяются различные растворители, вид растворителя указывается в паспорте лака).
Таблица 2
Растворитель | Температура кипения, °С | Температура самовоспламенения, °С | ГОСТ |
Ацетон | 56 | 630 | 2603-63 |
Бензол | 80 | 580 | 5955-51 |
Бензин | 80—120 | 230—260 | 443-56 |
Дихлорэтан | 83 | 413 | 5840-51 |
Керосин | 180-315 | 300 | 4753-49 |
Ксилол | 136,5—141,5 | 500 | 9949-62 |
Скипидар | 150-180 | 252 | 1571-66 |
Сольвент 1 сорт | 120—160 | — | 1928-50 |
То же, 2 сорт | 188 —250 | - | 1928-50 |
Уайт-спирит | 165—200 | — | 3134-52 |
Метиловый спирт | 65 | 475 | 2222-65 |
Бутиловый спирт | 116 | 366 | 5208-50 |
Этиловый спирт | 78 | 404 | 5962-51 |
К клеящим лакам относятся: карбонильный клеи, клей БФ (различных марок от БФ-2 до БФ-6), а также некоторые лаки. Высокой клеящей способностью обладают глифталевые лаки. Бакелитовый лак рекомендуется для склейки и пропитки каркасов гетинакса и текстолита. После склейки каркас следует прогреть при температуре от 120 до 135 °С для полимеризации лака (время полимеризации снижается с повышением температуры). Этот лак применяется также как пропиточный. Основное его назначение — покрытие пластин стали. Последнее рекомендуется выполнять распылением с повышенным количеством летучих, при этом лак проникает в поры окалины, хорошо охватывается с металлом и служит как защитой от влаги, так и электроизоляцией от вихревых токов. Покрывать густой лак кистью не рекомендуется, так как этим снижается заполнение стали магнитопровода и плохо заполняются поры в окалине Для быстрой склейки часто применяют шеллачный лак имеющий очень высокую клеящую способность, но при наличии тонких проводов его применять не следует ввиду его несколько повышенной гигроскопичности и кислотности; кроме того, шеллачный лак дорогой.
Воскообразные материалы, являясь гидрофобными, обеспечивают высокую влагостойкость пропитанных ими изделий и высокие электрические свойства. Влагопоглощаемость этих материалов практически равна нулю. Их недостатком является большая усадка при остывании, приводящая к появлению пузырьков воздуха в пропитываемых изделиях, и невысокая температура плавления. Целесообразно их применение при изготовлении трансформаторов для сырых помещений (насосные, котельные и др.).
Парафин имеет температуру плавления 50—55° С, церезин имеет температуру плавления 57—80° С (в зависимости от марки). Церезин дает меньшую усадку, чем парафин, температура его плавления выше, он меньше окисляется при нагреве. Все это обеспечило церезину более широкое применение, несмотря на его более высокую стоимость. Его рекомендуется применять для пропитки обмоток трансформаторов и картонных каркасов. Озеркит имеет температуру плавления 65—84° С, головакс — 93-130° С, но их электрические свойства ниже. Их можно применять для проварки картонных каркасов, деревянных крепежных деталей. Часто применяют комбинированные компаунды из указанных материалов, а также с добавлением канифоли и других компонентов.
Воскообразные материалы относятся к небольшому числу компаундов, которые могут быть применены в мелкосерийном производстве.